- The process of creating a drug - May 23, 2023
- How do scientists model mental disorders in animals? - May 23, 2023
A rotary evaporator, also known as a rotovap or rotavapor, is a laboratory device used for the efficient and gentle removal of solvents from samples by evaporation. It works by heating the sample at a low pressure, causing the solvent to evaporate and leaving behind the desired substance. Occasionally, the chemistry research literature will make mention of this technique and equipment, often referred to as a “rotary evaporator”, though it may also be alluded to by other terms (e.g., “the sample was evaporated under reduced pressure”).
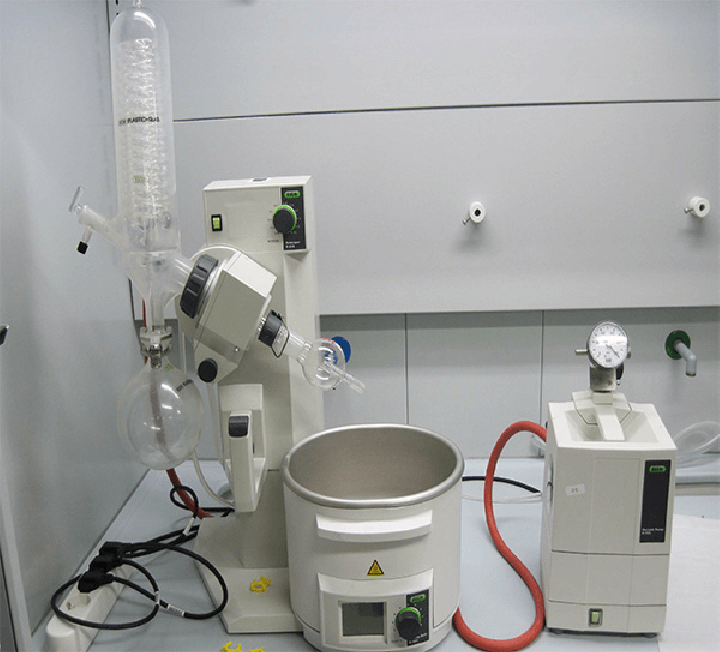
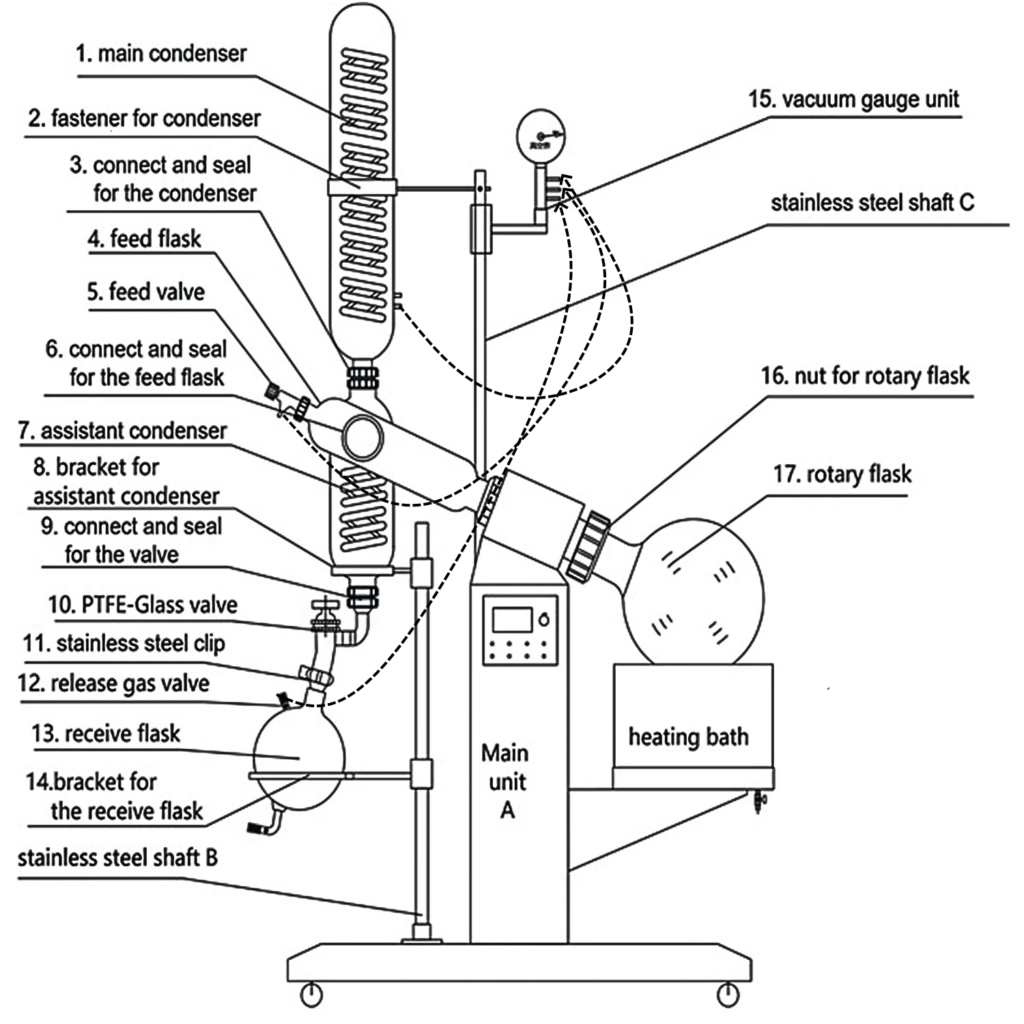
Rotary Evaporator Applications
The rotary evaporator has a wide range of applications in various fields, including chemistry, biology, pharmaceuticals, and food science. Some of the most common applications of rotary evaporators are:
1. Concentration of samples: Rotary evaporators are often used to concentrate samples by removing the solvent, allowing for a more concentrated sample to be obtained for further analysis.
2. Purification of compounds: Rotary evaporators can be used to purify compounds by removing impurities or other unwanted substances, leaving behind a purified sample.
3. Extraction of natural products: Rotary evaporators can be used to extract natural products from plants or other sources, allowing for the isolation of desired compounds for further analysis.
4. Analysis of volatile compounds: Rotary evaporators are often used to analyze volatile compounds in samples, allowing for a more accurate and precise analysis.
5. Synthesis of new compounds: Rotary evaporators can be used in the synthesis of new compounds by removing solvents and other byproducts, allowing for a more efficient synthesis process.
Overall, rotary evaporators are an essential tool for many laboratory applications and have a wide range of uses in various fields.
Principle of operation
Rotary evaporators serve a purpose due to the fact that decreasing the pressure surrounding a bulk liquid reduces the boiling points of its component liquids. In most cases, the component liquids used in rotary evaporation are solvents that need to be removed from a sample after an extraction or a step in an organic synthesis, typically without heating the delicate solvent-solute combination. Low boiling solvents like n-hexane or ethyl acetate can be easily separated from compounds that are solid at room temperature and pressure. However, careful usage of the instrument can also be used to erase a solvent from a sample that completely consists of liquids, provided there is minimal co-evaporation (azeotropic behavior) and the boiling points of the two liquids differ enough at the chosen temperature and pressure.
Higher boiling point solvents like water (100 °C at standard atmospheric pressure, 760 torr or 1 bar), dimethylformamide (DMF, 153 °C at the same), or dimethyl sulfoxide (DMSO, 189 °C at the same) can also be evaporated with a rotary evaporator if the unit’s vacuum system can reach a low enough pressure. For example, both DMF and DMSO will boil below 50 °C if the vacuum is reduced from 760 torr to 5 torr [from 1 bar to 6.6 mbar]. However, newer methods often take precedence over rotary evaporation in these cases (e.g., evaporating while centrifuging or vortexing at high speeds). Rotary evaporation for high boiling hydrogen bond-forming solvents such as water is usually used when other evaporation methods or freeze-drying (lyophilization) are not available, due to the tendency of these solvents to “bump”.
The key components of a rotary evaporator are:
1. A motor driving the flask or container that holds the sample material which is to be evaporated.
2. A vapor tube acting as a central axis for the sample’s rotation and providing a vacuum-tight passage for the vapor produced.
3. A vacuum system to reduce the pressure in the evaporator.
4. A heated fluid bath, such as water and oil, to warm the sample.
5. A condenser with either a coil circulating coolant or a “cold finger” filled with coolants such as dry ice and acetone, producing a cold surface, a type of cold trap.
6. A condensate-gathering flask at the bottom of the condenser to receive the distilled solvent once it has been re-condensed.
7. A mechanical or motorized apparatus for raising the evaporation flask from the heat bath in a rapid manner.
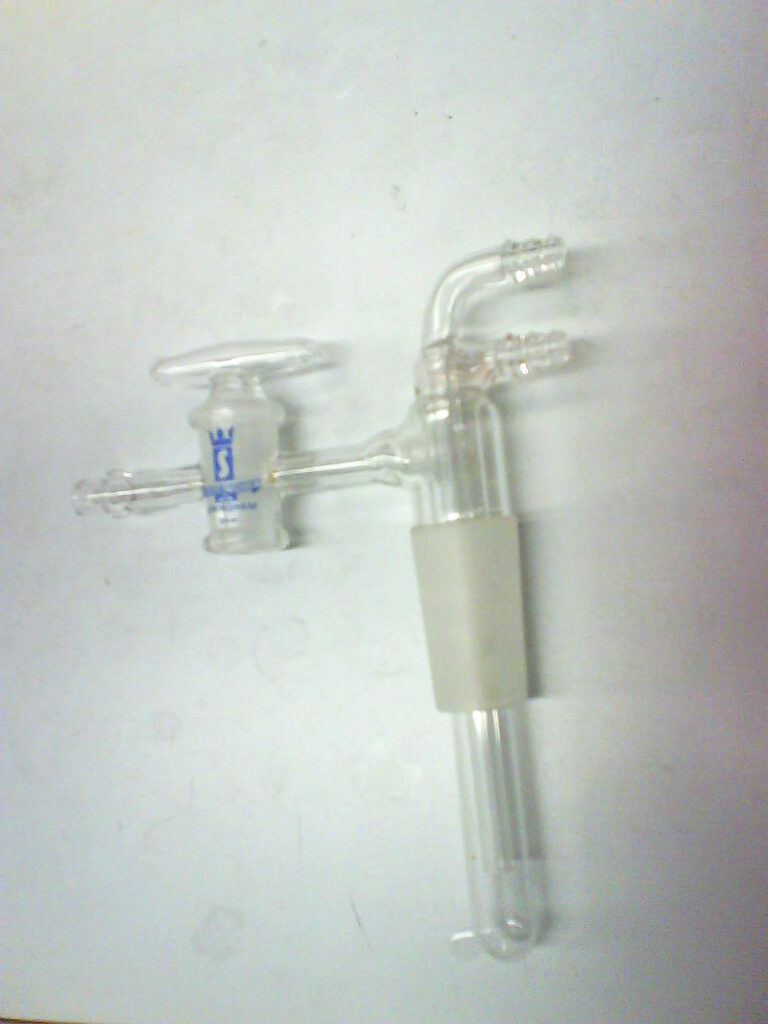
In the great majority of instances, a water bath is useful for laboratory purposes, however an oil bath is employed to vaporize high-boiling liquids. Particular oil mixtures act as a heat-carrier and make it possible to carry out experiments at a wide range of temperatures, from +5 to +360C. The most suitable heat-transporter for oil baths is colorless silicone oil (a combination of organosilicon compounds) that can hold up to long-term heating at temperatures up to 300 – 360C with no major change in color or viscosity. In some instances, after extended heating at the highest permissible temperature, the oil in the bath can flare up. In order to put out the fire, the bath is covered with asbestos fabric. Neither water nor sand can be used to put out burning oil.
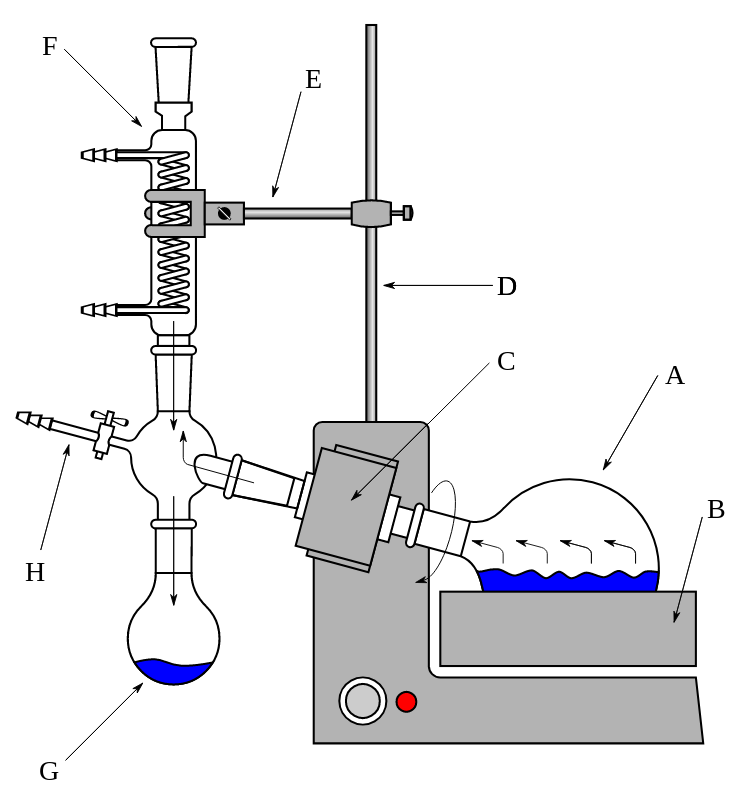
The rotary evaporator is constructed from a glass cylinder fitted with a slit, to which a round bottom flask A is connected and heated by a water bath B. A motor C powers the flask in rotation, and the solvent vapor enters the reflux condenser F, where it is cooled and condensed, flowing into the condensate-collecting flask G. The different parts of the rotary evaporator can be additionally attached with the help of a tripod D and foot E. A valve H is provided in the system for a fast vacuum release and is also often employed for introducing inert gas (argon or nitrogen) into the system.
The rotary evaporator works by reducing the boiling point of the solvent by creating a reduced pressure in its system utilizing either a waterjet or vacuum pump. This approach enables the solvent to be removed from the mixture at a lower temperature, avoiding the side reactions that can occur when the blend is heated.
What is the purpose of a Chiller in relation to a Rotovap?
Providing cooling and ideally a recirculating chiller, a chiller is necessary for a rotovap to ensure that the rotovap has proper cooling at the exact temperature. To evaporate the solvent correctly in the rotary evaporator, chillers are used to add cooling since the evaporated solvent is warm. Generally, a chiller will pump a cool liquid (commonly water or a mixture of water and glycol) to the process to take away the heat and the hot fluid is returned to the chiller. The chiller is connected to the reflux condenser and should be employed instead of using water to cool the reflux condenser.
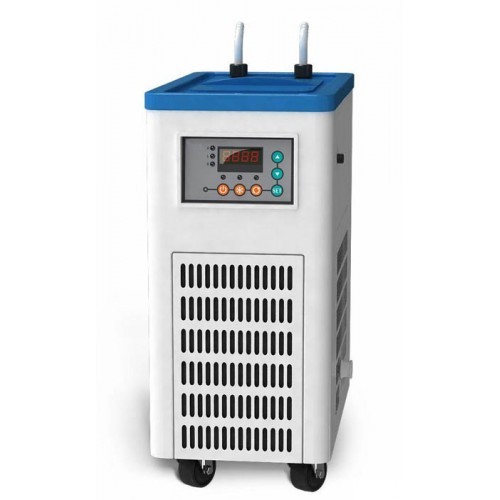
Accessory vacuum pumps
For most volatile solvent one can use a waterjet pump as in the image below. The force of the vacuum generated is determined by the speed and configuration of the fluid jet as well as the shape of the restricted and mixing sections, but if a liquid is employed as the operating fluid, the strength of the vacuum produced is restricted by the vapor pressure of the liquid (for water, 3.2 kPa or 0.46 psi or 32 mbar at 25 °C or 77 °F). If a gas is used, this restriction does not exist. Not taking the source of the working substance into account, vacuum ejectors can be notably smaller than a self-powered vacuum pump of the same capacity. Cost ranges from ~25-30$.
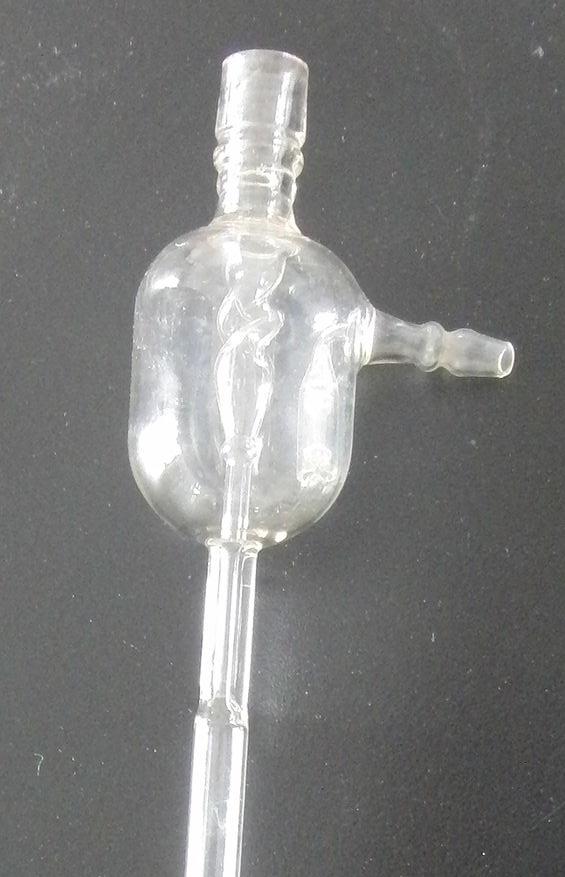
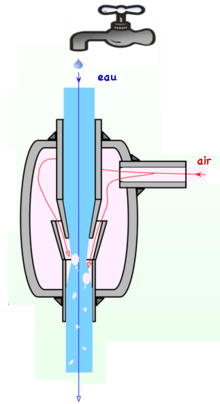
Alternatively, one can use a vacuum diaphragm pump which does not take a water stream and is easy to use. This type of pump may generate up to 1.5 mbar vacuum. Main disadvantage is the noise produced of 50-60 dB and the requirement of periodic maintenance (replacing oil and membranes). Moreover, diaphragm pumps cost from ~450-500$ and take up to ~200-2500W.
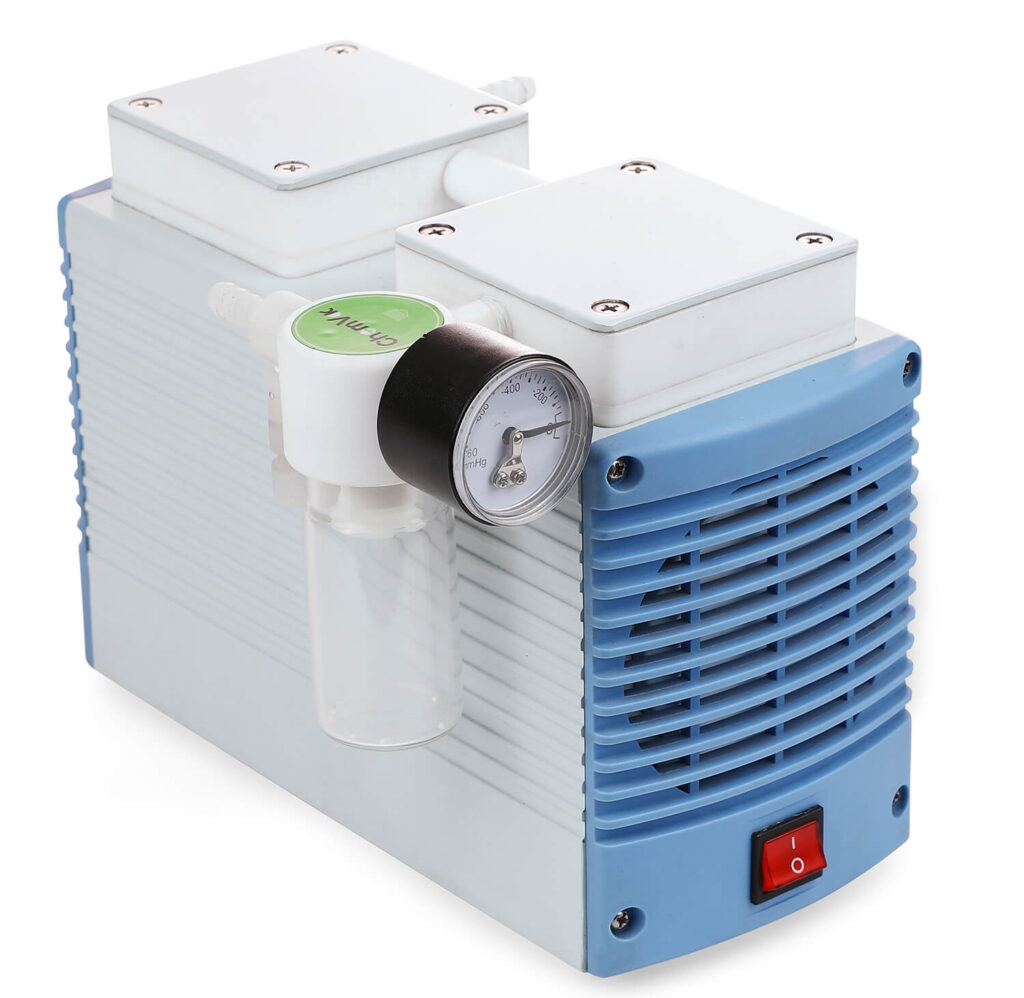
General rules for usage of a rotary evaporator
1. Before use, the collection flask of the unit must be cleared of any material to avoid the unintentional combining of incompatible chemicals.
2. The flask containing the solution is put onto the rotary evaporator. A bump trap is used to stop the solution from splashing into the condenser and becoming contaminated. It is strongly suggested to start off with a clean bump bulb just in case anything spills. This would let the experimenter retrieve the solution or solid.
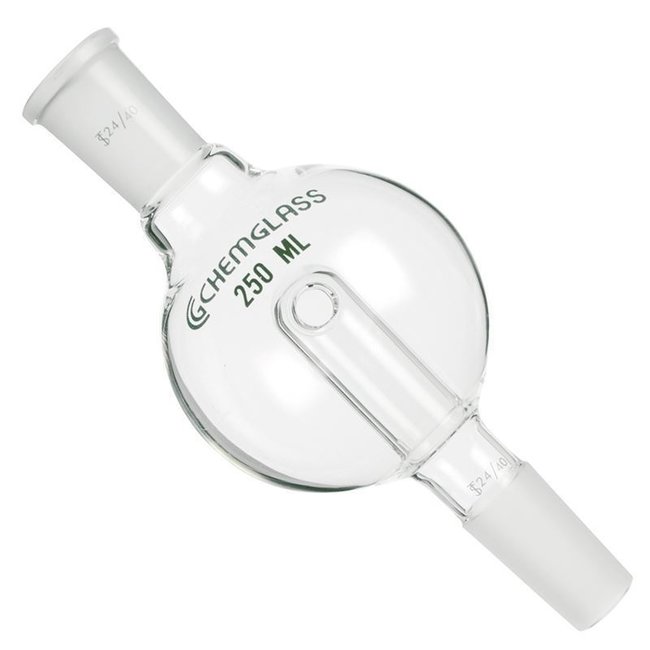
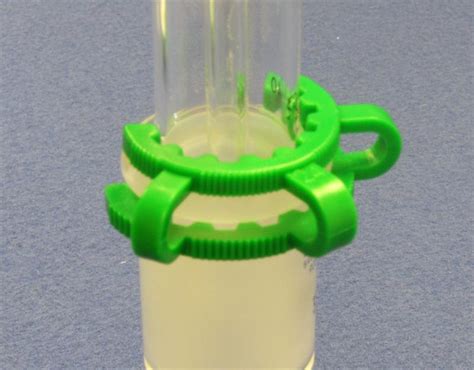
3. A metal or Keck clip is used to fasten the flask and the bump trap. The green one shown below fits 24/40 ground glass joints. The blue clips fit 19/22 joints and the yellow ones fit 14/20 joints, which are likely to be used in the lab.
4. The knob on the motor is used to control the rotation speed of the flask. A general rotavap works with a variable speed sparkless induction motor spinning 0-220 rpm and providing high constant torque. A good setting here is 7-8.
5. The aspirator vacuum is activated. On most models, the vacuum on/off control is managed by rotating a stopcock on the top of the condenser (left side of the diagram above). This stopcock is then used to release the setup after the solvent is removed (see point H on the scheme).
6. The flask A is either lowered into the water bath or the water bath is lifted to submerge the flask in the warm water. On most models, a convenient handle (with height locking mechanism) shifts the entire condenser/motor/flask assembly up and down. Usually the tilt of the condenser assembly can also be adjusted. The water bath temperature should not exceed the boiling point of the solvent!! For small amounts of common solvents the bath heater is not needed.
7. The solvent should begin to accumulate on the condenser F and trickle into the receiving flask G. Some solvents (such as diethyl ether or dichloromethane) are so volatile that they will also evaporate from the receiving flask and be discharged down the drain. OPTIONALLY: To prevent this, a cooling bath on the receiver or (on some models) a dry-ice condenser can be used. Additionally, an extra trap (with dry-ice or liquid nitrogen) can be positioned between the vacuum source and the condenser unit. This is especially important of a membrane pump is being used as the vacuum source. There is a rotary evaporator with dry ice cooler for low boiling solvents such as diethyl ether.
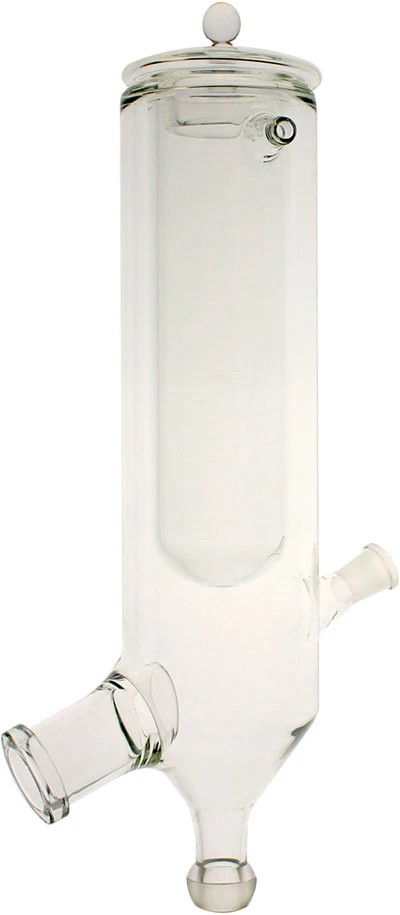
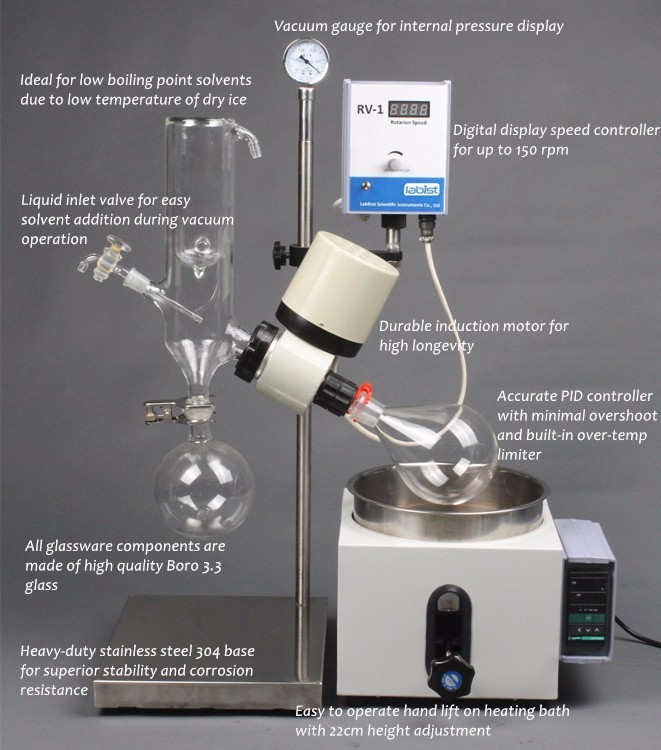
8. Once the liquid has evaporated (or whatever the desired result is), the vacuum must be gradually released to avoid any breakage of glass. The flask must be removed from the water bath and spinning should be stopped.
9. The bump trap needs to be wiped down and the receiving flask must be emptied once the evaporation is finished.
Tips and Tricks
To avoid the build-up of limescale which accumulates on heating elements like the thermistor and coils, it is best to use distilled water in the bath. Additionally, regular tap water can cause colonies of unsightly algae to form, particularly in summer. To avoid this problem, it is recommended to regularly replace the water.
To eliminate gunk from the coils of a water condenser, the condenser must be detached from the rotavap and submerged in a weak nitric acid solution for several hours. After cautiously washing the inside, it’s time to reassemble the rotavap. Take all the necessary safety precautions when handling nitric acid!
The ground glass joint that supports the flask does not need to be greased, although on rare occasions it (or the bump bulb) might become stuck. Some companies offer special joint clips that can easily loosen stuck joints by rotating them in one direction.
If you don’t have one of these tools, try gently moving the joint from side to side. Finally, if a mechanical pump is used instead of an aspirator to produce a vacuum, a secondary trap must be used to prevent the solvent from damaging the membrane or being absorbed in the oil.
Safety
The potential risks may include implosions caused by the usage of glassware with flaws, such as star-cracks. Explosions may arise from concentrating unstable elements when concentrating liquids through the rotary evaporation process, such as when evaporating a peroxide-containing solution. This may also take place when concentrating certain unstable compounds, such as organic azides, acetylides, nitro compounds, molecules with strain energy, etc.
Those using rotary evaporation equipment must be mindful of the danger of entanglement with the rotating parts, particularly in regard to loose clothing, hair, or necklaces. In this case, the winding action of the spinning parts could draw the user into the device, resulting in shattered glass, burns, and chemical exposure. Extra caution is also necessary when operating with air-reactive substances, in particular when under vacuum. A leak can draw air into the machine, which can lead to a violent reaction.
Additional equipment
There are various types of nozzles, like the spider, equipped with various flasks. These are situated after the bump trap on the outlet of the rotary evaporator.
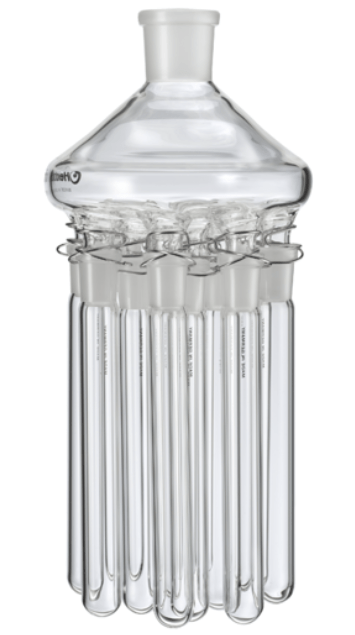
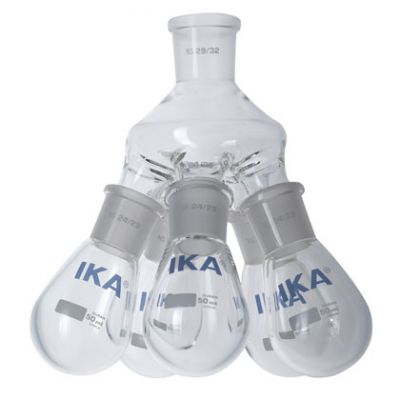
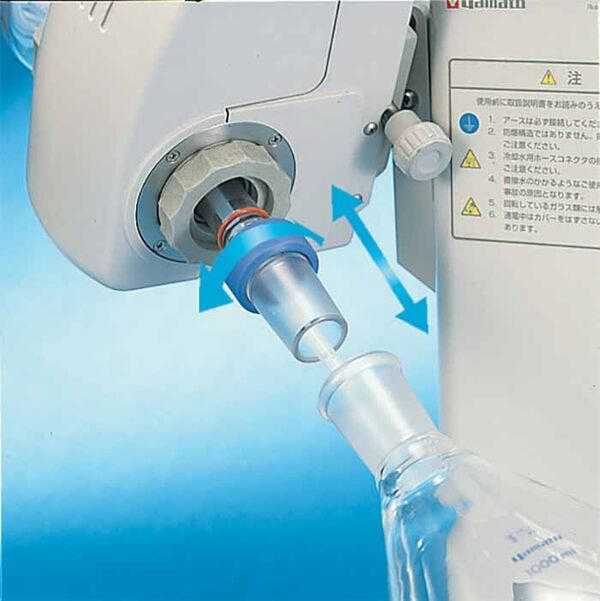